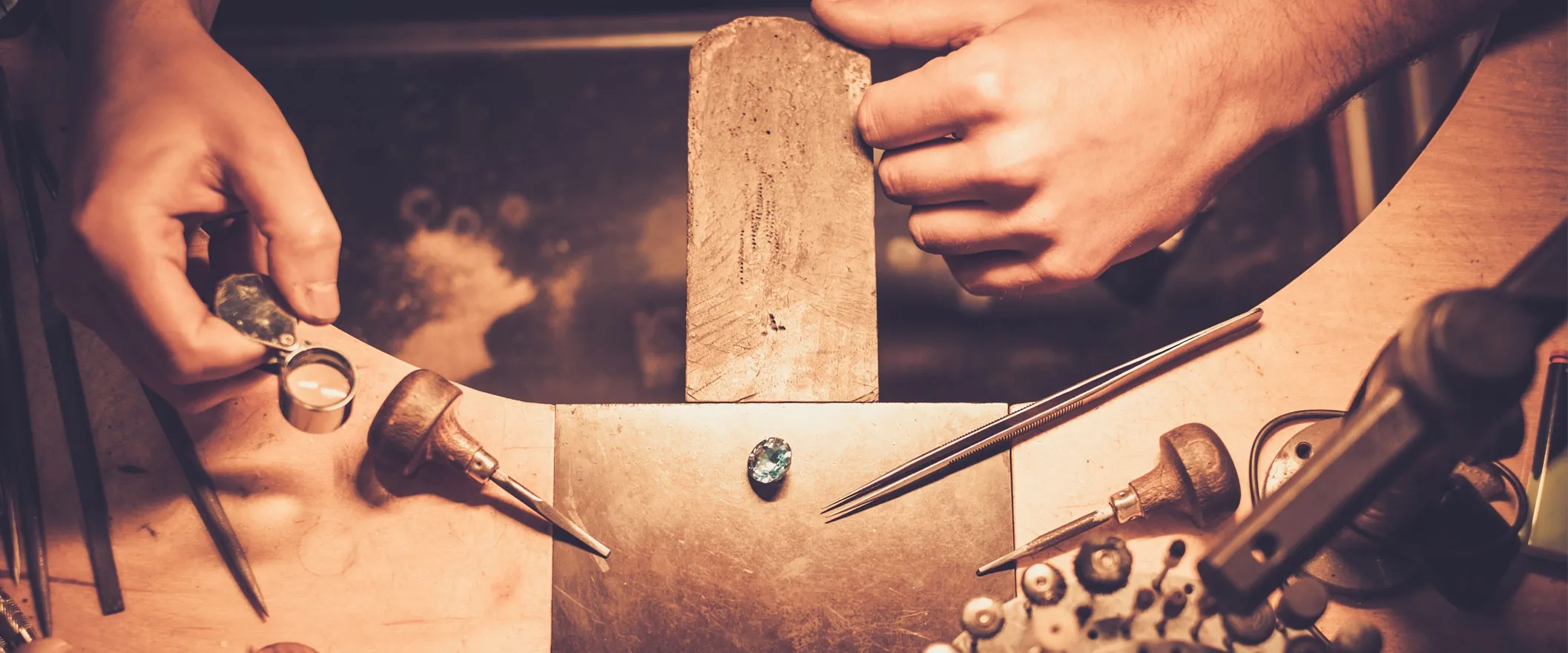
Custom Jewelry
Discover the ins and outs of the custom design process at Joe Escobar and see what it takes to create unique jewelry.
Custom Jewelry Design
Design your own jewelry in 3 easy steps. Creating your own jewelry is a simple process whether you design online or in person at our store.
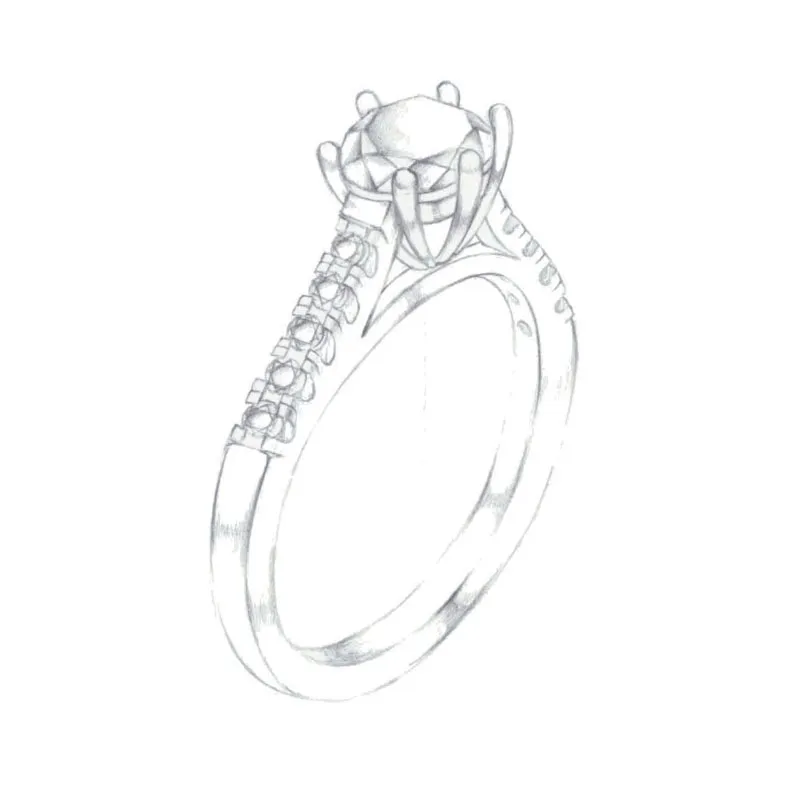
Custom Design
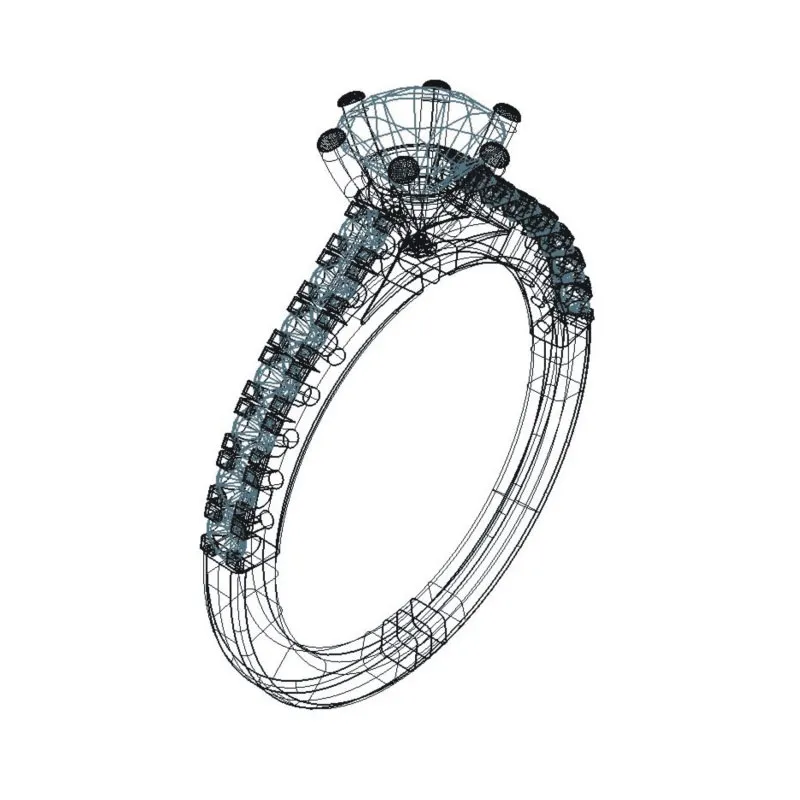
Modeling
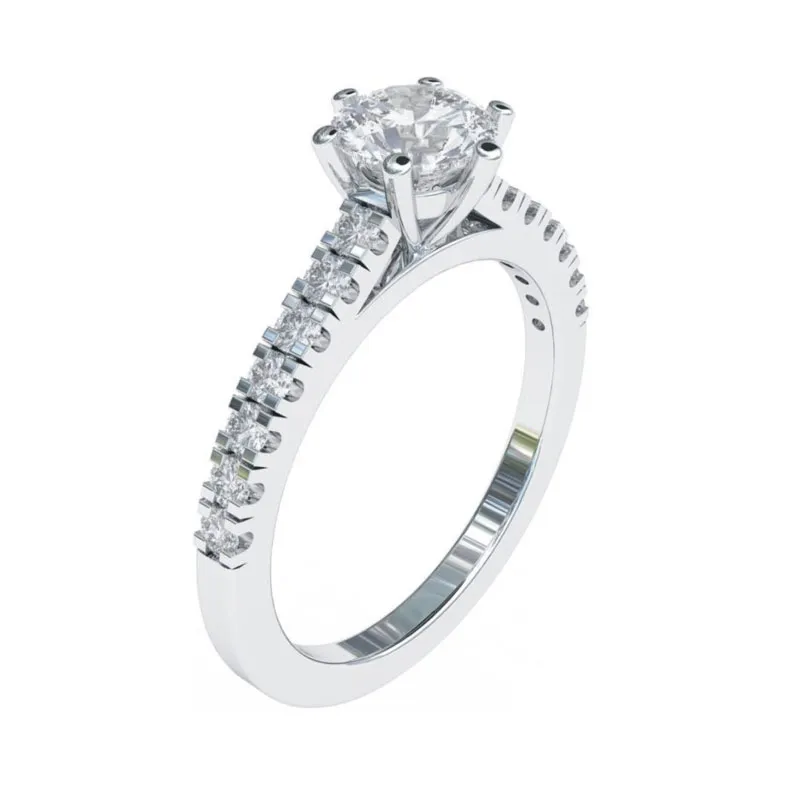
Production
Why Custom Design?
If you could create a piece of jewelry for a loved one, what would it look like? Would it reflect their unique personality, even those quirks you adore? Are you having trouble visualizing it? We can help with all of that.
At Joe Escobar Diamonds, we specialize in custom jewelry work, and in translating client ideas into beautiful works of art. Our custom-designed rings are one-of-a-kind creations that will give you years of enjoyment.
Our Process
We will make the entire process incredibly fun and rewarding. We don’t want to just fulfill your expectations, that’s too easy — we want to surpass them!
To explain our process, we invite you to read through our day-in-the-life custom story, and view the videos. Both walk you through a custom ring being made, from start to finish. We think it will help you better understand the process, the work involved, and yes, even how much fun it can be. Behind the scenes, our designers/artisans spend hours making sure that our custom work is flawless when delivered, and we have a rigorous quality control process to ensure that your piece will last for generations to come.
Visit Us Today
We know that creating a custom piece is a massive decision. We have experts ready to help with any questions or concerns you may have and guide you into the world of custom jewelry design with ease.
Silicon Valley Engineer finds his Diamond, and Proposes
We first met Chris a few months ago. He was planning to propose to his long-time girlfriend, and wanted to see loose diamonds so he could make a decision on a diamond ring that would ‘wow’ her. As an engineer in the heart of Silicon Valley he did his homework - and then some.
We showed him dozens of loose diamonds of different qualities and cut aspects. He finally found the diamond that he thought was perfect for his soon-to-be fiancé. Knowing that there were a multitude of rings to choose from, and not being positive of the style that she would love, we set the diamond in a beautiful thin-style solitaire. This allowed Chris to make his presentation a surprise, and know that ultimately she would get exactly what she dreamed of.
When we met fiancé Sarah a week after Chris proposed, she was still tearing up as she recalled how Chris proposed to her.
The Consultation - He said, She said, and We Listened
We explained to Sarah that the best way to find the perfect style is to try on as many rings as possible. We could tell she liked this idea. During the next hour, we brought out dozens of rings, she slipped them on and off her finger, moving throughout the various styles in our showcases. Little did she know, that we were taking note of Sarah’s likes and, just as important, her dislikes. We were paying close attention to colors, textures, widths, and even how some styles made her feel – we could see it in her expression. Jewelry can evoke powerful emotions, memories of relatives that wore similar rings, heirlooms that have been passed down through the generations … and the stories that come with them.
In this first meeting, we discovered that she liked a ring that had a modern styling with antique details – it seamlessly blended the Belle Époque jewelry period with a contemporary flair. Sarah was attracted to what we call a ‘Halo’ effect around the center diamond that sits nice and low to the finger. She is in her mid-twenties and very active and wants a ring she can wear daily with little fear of catching it on clothing and other things. She also loves a delicate band on her hand with small diamonds set down the sides, all designed to accentuate the center stone.
Now that Sarah is in love with a style, and comfortable in that knowledge, it is time to call it a day. We have all the notes that we need to start the process, so it is time for Sarah to go home and digest all of the information that she received today.
The Design - Three Rings in One
The next weekend as we were finishing up with another client, Sarah appeared at our showroom. She was smiling ear to ear! “What’s going on?” we asked. She responded, “I have given it a lot of thought….and I am sure that is going to be my ring!”
The staff of Joe Escobar Diamonds got right to it. In consultation with Sarah, we narrowed the design elements down to three rings. She liked the basket that holds the diamond from one, the band from a second, and the prong work from the third. But this was no problem for our design staff – we recommended custom making the ring, our only issue was that we didn’t have an existing ring for her to see how the design elements would come together. Luckily, we had a solution. We suggested that we create a drawing of the final piece, and while this is not something we do for every custom ring design, we suggested commissioning one of our in-house artists to put our concept to paper. Within 72 hours, we had a drawing and asked Sarah to come to the store to review it. We can see the combination of excitement and anxiety on her face. With a little bit of hesitation, we slide the concept drawing of the ring across the counter. Her face immediately lights up! “I LOVE IT!!!” she says, and goes on to say “It’s exactly what I envisioned!” And that’s great news to us, we love to hear that.
Next up, we began creating a three-dimensional model of the ring from the drawing, so Sarah could actually try it on.
Waxing Poetic - Lost-Wax Casting
There are several different ways to make a ring. The method that we have chosen for this particular project is lost-wax casting, which the French sometimes call ‘cire perdue.’ It is a process by which a metal (such as silver or gold) sculpture is cast from an artist’s rendering. Intricate works can be achieved by this method, and best of all, it enables the client to try on a wax model of the ring. She can then make any changes necessary to the width, height, and even diamond size before the ring is finished.
As we begin the meeting with our head jeweler, the differences between our staff/management could not be more apparent. We are the dreamers - and our design team the architects and engineers. We have assembled the perfect team for a creative endeavor. The head jeweler takes our talk of “feel” and “height” and magically transforms it into millimeters, angles, and percentages. Before long, he tells us the raw materials he will need: 20 diamonds measuring 1.5 mm each for the halo; 12 diamonds measuring 1.1 mm each for the under gallery; and 16 diamonds measuring 2.0 mm each for the band.
Our jeweler hand carves the ring out of a solid block of wax. This wax model has all of the actual diamonds in it to show precise detail of the scale of the ring after it is finished.
This model is used to judge the height off of the finger, width of the band on the finger, and proportion of side diamonds to the center. Because of this, he needs the diamonds before he can start. The wax model is tailored specifically for the size of each center diamond and for every single side stone.
Selecting the Diamonds
When custom making a ring, or any piece of jewelry, it is imperative that all the diamonds are precisely matched, not only in quality, but also most importantly in size. The 4Cs of diamond quality are color, clarity, cut and carat weight - this is the universal method for assessing the quality of any diamond, anywhere in the world. With every piece of custom jewelry that Joe Escobar Diamonds produces the diamonds are sieved for approximate size, and then hand calibrated to match perfectly. We believe this extra step ensures that every piece of custom jewelry that we produce be as perfectly straight as possible. When the side diamond size varies (even as much as a tenth of a millimeter) it can cause the band of the ring to look wavy and uneven.
With this in mind, we begin the task of selecting the diamonds that will go on the sides of Sarah’s ring. Her center diamond is an F color (meaning colorless on the color scale) and a VS2 clarity (very very slightly imperfect), so the quality that we have selected to use for the accent diamonds is F color and VS clarity. (Learn more about this in our Diamond Education section) Even though we are using almost 50 diamonds total in the sides of her ring, we examine every single one of them under magnification and then measure them with a digital caliper.
Sculpting your Ring
With the diamonds selected and delivered to the custom jeweler, the wax carving process can now begin. Starting with a block of wax like a sculptor does with a statue, this process requires foresight and a vision. The jeweler uses a pen to mark out exactly where he wants to make the initial incisions. This is a long and complex process taking between three and five hours depending on the complexity of the piece. Two-toned pieces (having both platinum and yellow gold) are cast in separate pieces and require separate wax models for each section. Our staff periodically checks in on the process and offers any insight necessary, when the jeweler needs a consultation on the design or on Sarah’s expectations.
The custom jeweler begins with a long cylinder of blue wax, sawing off the large block that he will use to shape the ring. The next step is to calculate the millimeter diameter of the finger size and hollow out the center section. He stops about a ¼ size short as this will allow the inside of the ring to be polished during finishing, ending with the perfect ring size. First the jeweler measures the size of the center diamond and the size of the accent diamonds that will be going in the Halo. With these measurements he calculates how wide the overall Halo will be. After these measurements are confirmed, he uses a compass to scratch the outline into the top of the wax block. With the outline in place, he blocks the edges to the sides of his outline. He then lays the diamonds for the band on the block and measures out the width of the shank as well. During all of this he is concentrating solely on the center points of the Halo and band, this is imperative to ensure the ring is laser straight.
The jeweler then sculpts the wax into the circular shape of the halo, and also trims the wax to the edges of the band. It is at this point that the wax model is starting to resemble an actual ring! The wax is further refined and the edges are rounded off nicely, and the diamonds are again placed on top to ensure that the size is perfect. As this is checked using a microscope, the jeweler uses surgical precision to cut out the under gallery leaving only the support bars in place, each equal length, and symmetrical widths.
The diamonds are then set into the wax and prongs are fashioned to hold them. These wax prongs are purely cosmetic, and are only used to hold the diamonds to the wax model so that it can be tried on. This will aide Sarah in visualizing what the ring will look like when it is finished.
Securing your Approval - Wax Model, Meet your Client
With the wax model complete and all of the diamonds in place, Sarah can now come in and try on a model of the ring. The wax is a blue color, so sometimes that can be a little disconcerting. We tell clients to always observe the structure of the ring, placement of the diamonds, and the general proportions. Another thing that we mention to Sarah is that when we do wax casting, the wax model actually becomes the ring. Because of this, the wax will look slightly thicker and heavier than it will in the finished ring. We need to cast a little bit more than we actually need, so that when the ring is in the finishing process the jeweler has enough to be able to shape and polish the metal. We can tell from the look on Sarah’s face when we first sit down that she has some reservations about how the wax is going to look.
We know instantly that the wax model is what we were both envisioning as the look of trepidation is instantly replaced with elation as we place the ring in her hand. “Yes!” she exclaims as she gently slips the ring onto her finger. “The height is exactly what I was thinking!” We smile as she says this, a process that is familiar to us, having custom-designed hundreds of rings for Escobar clients over the years. Every time a client tells us they love a design we’ve created, it fills us with great pride in being able to take someone’s vision and make it real for them. We talk about the proportion of the diamonds in the Halo to the center diamond and decide that the size complements the center perfectly. Sarah indicates that she would like the band a touch thinner, and I assure her that it will look thinner in the finished metal. I also let her know that the band is already very dainty and to go even thinner with the size of the halo and her center stone could cause the ring to not be as strong as a daily-wear engagement ring should be.
We go over the diamonds in the band, and while we initially wanted the diamonds to go ½ way around, we both decide that we will see a little too much metal on the sides and opt to add two more diamonds on each side to have the diamonds go ¾ of the way around.
With that last detail in place, we schedule another meeting with our custom jeweler to impart the minor changes that we would like done to the wax model of the ring. Given that the changes are minor, Sarah will not have to come back in to see the wax model again. If the changes were substantial we would schedule another appointment to meet and review the wax model a second time.
Casting - Pouring the Platinum
The custom jeweler makes the necessary minor modifications to the ring and sends the ring out to casting. Casting is the only component of the custom process that is not done in-house at Joe Escobar Diamonds. The wax model is sent out to the casting company and is put through a series of steps to convert that wax model into platinum! In order to cast a ring, a negative impression is needed. A sprue and button are added to the bottom of the wax model - these act as a channel to pour the platinum into later in the casting process.
The wax model with the new sprue and button are placed into a metal cylinder. An investing media (a plaster of paris type material) is then mixed and poured into the cylinder around the wax model. A vacuum table is then used to remove all of the air bubbles in the investment media. Once the media has set, the metal cylinder is placed upside down in a burnout oven.
This oven liquefies the wax model and removes it from the media leaving a perfect hollow of the wax behind. The wax ring is lost during this process, hence the term “lost wax casting.”
The investment is then heated in a kiln to a specific temperature and placed in a centrifuge. The platinum is melted in a crucible next to the investment and when fully liquefied the centrifuge is released and metal forced into all the hollows of the mold. Platinum is an incredibly dense metal, in fact it is the third densest metal on the planet! The centrifuge hurls the platinum into the investment at speeds up to 60 miles per hour! The still hot investment material is then quenched in water and due to the rapid temperature change fractures away from the metal casting. What is left is a metal version of the wax model!
Finishing Up - Tumbling, Spinning, Pre-Polishing
When we receive the cast ring back from the casting company, it is still pretty rough and has a long road ahead of it before it will grace Sarah’s finger. the first thing that we do when we see the casting, is put it through quality control. This is a critical step in custom jewelry as it ensures against structural and casting defects that can compromise the integrity of the ring. We examine every nook and cranny of the ring under a microscope with magnification ranging from 10x to 30x. Once the casting passes with flying colors, we deliver the ring to the custom jeweler. Out of the five full-time jewelers that we have here on premise at Joe Escobar Diamonds, two are dedicated solely to custom work.
While we’re getting close to a finished piece, the finishing process is complex. First the newly cast ring is placed into a tumbler. A tumbler is basically a machine that spins metal filings around at high speed. This smooths out the rough edges of the casting and helps with pre-polishing. After the casting has been tumbled for approximately one hour, the custom jeweler removes it and brings it to the bench. The finishing jeweler then uses a file and sandpaper to further form the casting, smoothing out the extremely rough sides, and blocking off the edges. This step is critical as any variations in the casting such as asymmetry, bad edges, and width variations, can be addressed immediately. The casting is then pre-polished in order to bring the platinum to a shine. It is critical to pre-polish the ring before the diamonds are set, as after the diamond setting process. some of the areas are inaccessible.
Setting the Diamonds - the Seat, the Prongs, the Perfect Symmetry and Strength
The casting is now ready to have the diamonds set. The prongs, especially for the center stone are things that Joe Escobar Diamonds does not cast in place. This is because the prongs are much stronger when they are hand drawn wire. This extra step takes additional time on the ring, but given the added security to hold the center diamond tightly, we feel is well worth it.
Using a microscope, the jeweler drills a hole so that each diamond has a “seat”. The jeweler then uses metal that is displaced from drilling at the top of the drill hole, to form prongs. This continuous piece of metal is many times stronger than a prong that is welded on. To do this process, the jeweler uses a compressed air powered “Graver”. this incredibly precise tool allows the jeweler to make perfectly symmetrical micro-prongs, and ensure that the diamonds are held securely. To make sure the prongs are perfectly cut, the blade of the Graver must be sharpened by hand before each use.
Quite a few hours later, when all of the ‘pave’ set diamonds are positioned in place and tightened, it is finally time to set the center diamond. The prongs that hold the center stone are drawn out of solid platinum wire. The jeweler takes a thicker wire and compresses it multiple times making it very dense. This adds a tremendous amount of strength to the metal and gives the prongs added durability. The prongs are then cut to size and welded into the Halo with a specialized laser welder.
Once the diamonds are set, the ring is polished in multiple stages, with different compounds and different polishing wheels, bringing the metal to a mirror finish. At this point any flaws in the casting would be apparent, which is why it is incredibly important to quality control the casting immediately.
When the jeweler shows our internal team the completed ring, we are confident that Sarah will love it! The curvature of the band, the rounded Halo, the height off the finger…everything is exactly as we discussed!
The Presentation - Appraised, Boxed Up, Ready to Wow
The ring is all finished, we have also finished the appraisal, with the ring tucked away in its box. Sarah is on her way into the store, and we all share her excitement. She is about to see all the hours of work on this custom project come to fruition. As she walks through the door with Chris, we can tell that she is excited. “I couldn’t sleep last night!” she exclaims. “I’m so nervous!” We can tell that Chris is apprehensive as well, as his only concern is her happiness with the finished product.
As we open the ring box, we see nervousness and apprehension disappear instantly to be replaced with elation, and followed closely by tears. “It’s the ring I’ve always dreamed of!” she exclaims as she gives Chris a hug and kiss, “and it fits perfect! I love it!” As if the look on Sarah’s face wasn’t enough, her words were music to our ears. When we deliver a finished custom ring, “perfect”, “love”, and “beautiful” are the words that let us know that we have not only met our client’s expectations, but surpassed them!
At Joe Escobar Diamonds, we find it incredibly rewarding to be such a big part of a couple’s life, and a privilege that they place their trust in us for a piece that will symbolize their bond of love for years, and even generations. We keep this in mind every time we help design the ring of someone’s dreams.
Come in, sit down. Let’s design something amazing — together.
Still Have Questions?
Creating a custom piece is a big decision, and we want you to feel comfortable. We’re here to answer any questions you might have!